Volta-Galvani Controversy
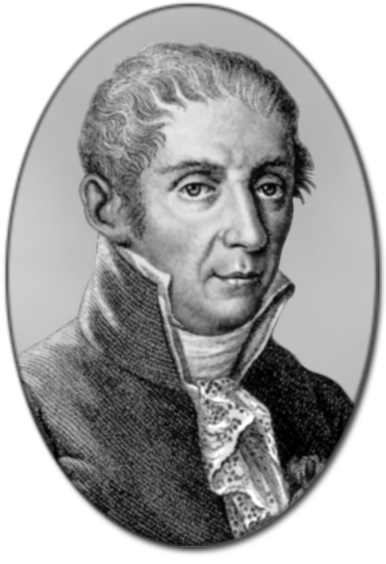
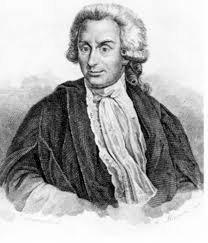
A scientific disagreement between Alessandro Volta and Luigi Galvani, known as the Volta-Galvani controversy, centered around the interpretation of a fascinating phenomenon observed in the late 18th century. This dispute led to significant advancements in our understanding of electricity and ultimately to the invention of the first battery.
The Frog Leg Experiment
In the 1780s, Luigi Galvani, an Italian physician and physicist, discovered that a dead frog’s leg would twitch when touched by two different metals 1,3. This observation sparked a scientific debate that would last for years and involve many prominent scientists of the time.
Conflicting Interpretations
Galvani’s “Animal Electricity”
Galvani interpreted his findings as evidence of an inherent “animal electricity” stored in the muscles and nerves of animals 4,6. He believed that the metal implements were merely connecting two separate reservoirs of this electric fluid, allowing it to flow and cause muscle contractions.
Volta’s “Contact Theory”
Alessandro Volta, on the other hand, was skeptical of Galvani’s interpretation. He repeated Galvani’s experiments and concluded that the electricity was not coming from the animal tissue but from the contact between the two different metals 3,6. Volta believed that the frog’s leg was simply acting as a sensitive detector for this externally generated electricity.
The Debate Intensifies
The disagreement between these two scientists led to a publication war that engaged many European scientists 7. Both Galvani and Volta conducted numerous experiments to support their respective theories:
- Galvani performed experiments showing that frog legs could twitch without the use of metal wires, supporting his “animal electricity” theory 7.
- Volta developed his “contact theory” and began experimenting with different combinations of metals to produce electricity without animal tissue 6.
Resolution and Legacy
While Galvani’s specific theory of “animal electricity” was ultimately disproved, his work laid the foundation for the field of bioelectricity and contributed to our understanding of nerve function 3.
Volta’s interpretation, though not entirely correct, led him to invent the voltaic pile in 1800 – the first electrical battery 3,6. This invention revolutionized the study of electricity and paved the way for numerous technological advancements.
Linguistic Legacy
The scientific community recognized the contributions of both scientists:
- “Voltage” comes from Volta’s name and refers to electrical potential difference 6.
- “Galvanism” originally referred to the generation of electric current by chemical action, as Volta described it 8. Today, it’s used in various contexts related to electricity and sudden stimulation.
These terms, while not interchangeable, both honor the work of these pioneering scientists and their pivotal roles in the development of electrical science.
Citations:
- On Artificial and Animal Electricity: Alessandro Volta vs. Luigi Galvani
- Luigi Galvani – Wikipedia
- The Frog Battery: A Misstep that Sparked a Revolution | EPBA Europe
- Galvanism – Creatures of Thought
- Galvanic cell – Wikipedia
- Luigi Gaalvani (1737- 98) Alessandro Volta (1745-1827) | A History of Science
- Original Sin – PMC, Bioelectricity
- Galvanism – Wikipedia
- Voltaic (or Galvanic) Cells- Generating Electricity from Spontaneous Chemical Reactions – LibreTexts
- The Controversy Between Galvani and Volta Over Animal Electricity: The Second STAGE
- The Galvani-Volta controversy
- March 20, 1800: Volta describes the Electric Battery
- Inspiring Frankenstein – The Body Electric
- Galvanic (voltaic) cells (video) | Khan Academy
- The Investigations and Inventions of Volta | American Scientist
- The Controversy on Animal Electricity in Eighteenth-Century Italy: Galvani, Volta, and Others
- Libretexts Electrochemistry/20.4:_Cell_Voltage
- 11.1: Galvanic Cells – Chemistry LibreTexts
- Electrodes and voltage of Galvanic cell | Chemistry | Khan Academy
- Electrodes and voltage of Galvanic cell (video) | Khan Academy
Copyright © 2025, Douglas E Powell